How a new drying technology meets cycle requirements while significantly reducing energy consumption.
Coatings of component surfaces must be dried immediately after application. Simple hot air blowers, as still used today in many processing plants, vaporize the adhering water at 85 degrees Celsius on the surface. The disadvantage here is that the heating of the components results in drying spots, which make downstream assemblies such as soldering processes more difficult or even impossible. At the same time, the components do not dry within the required cycle time of seven minutes.
In addition to the constantly high energy consumption, the handling of the extremely hot components also represents a major challenge.
Condensation drying – a gamechanger
The complete drying system at the Helmbrechts production site was converted to two rack dryers in a one-year development and test phase and in close cooperation with Harter, a drying system manufacturer from the Allgäu region. To design the new drying technology in the best possible way for our projects, materials, and customer specifications, a number of sample parts were successfully tested for different parameters at Harter’s technical center first.
The result: Thanks to its alternative physical approach, condensation drying can work in a lower temperature range between 40 °C and 75 °C. State-of-the-art integrated heat pump technology makes the system more efficient than other drying processes. Drying times are therefore often even significantly below the specified cycle times. In our case, a heat input of just 60 °C results in drying times of just four minutes – without any spots at all.
Hardly any energy loss
Both dryers are made of polypropylene and have an automatic lid system that opens just to move the product carriers in and out. Valuable heat remains in the system during drying and neither exhaust air nor moisture loads can occur.
Based on previous results, we decided together with Harter to set the drying at 60 °C. The short drying times and lower temperature prevent the component from being exposed to strong thermal stress and heating up. The surfaces heat up to just 45 °C and can therefore be further processed immediately.
The condensation drying system with its heat pump technology is also impressive in terms of energy: The rated power in production mode for the newly installed system is 6.8 kW and 8.2 kW respectively for each system. An incredibly low value, with a significant increase in quality.
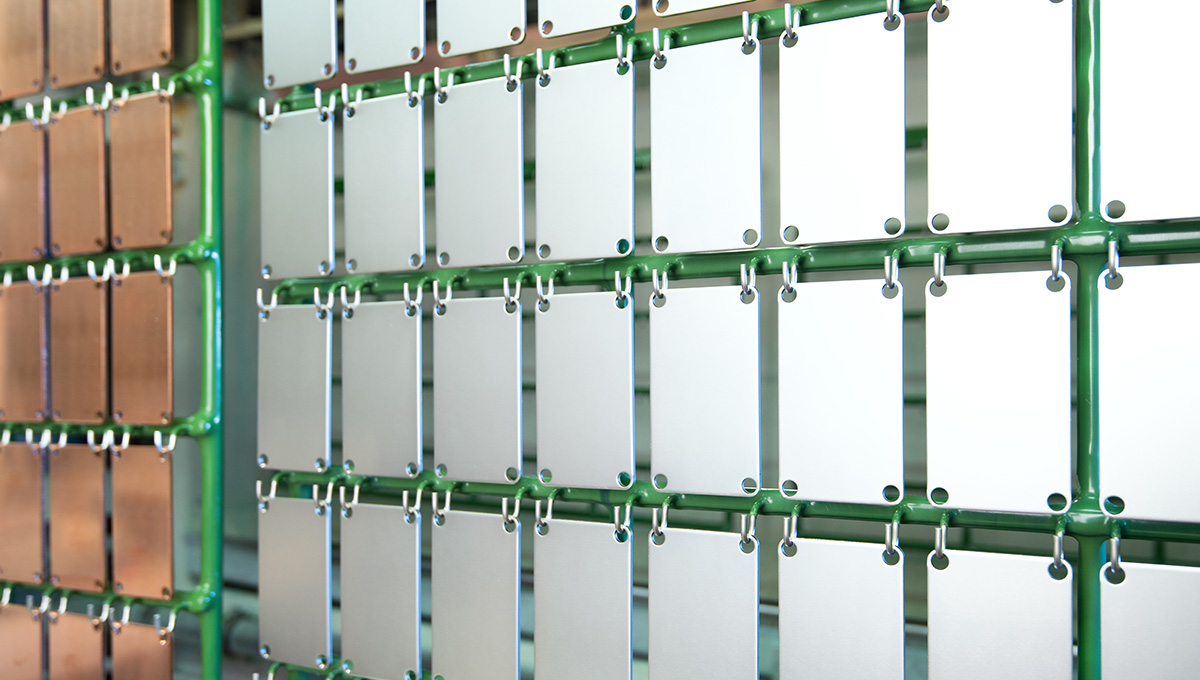
Completely exhaust free
The new dryers feature an integrated recirculation system with individual airflow. Four or six recirculation fans are installed in each dryer to generate the appropriate air volume flow. All dryers are equipped with special blow-off nozzles that blow off the first large water load from the often complex components when the goods carrier is moved in.
In a completely closed circuit, the required process air is first prepared in an Air genex® dehumidification module, then passed over the part’s surface at a high speed. This dry air absorbs the moisture very quickly and cools it in the dehumidification module until the water condenses. The air is reheated and recirculated back into the dryer. This combination of closed circuit and complete absence of exhaust air is unique on the market.