Wie eine neue Trocknungstechnik Taktvorgaben erfüllt und gleichzeitig den Energieverbrauch deutlich senkt.
Beschichtungen von Bauteiloberflächen müssen unmittelbar nach dem Auftrag getrocknet werden. Einfache Heißluftgebläse, wie sie bis heute noch in zahlreichen verarbeitenden Betrieben eingesetzt werden, verdampfen das anheftende Wasser bei 85 Grad auf der Oberfläche. Der Nachteil: Durch das Erhitzen der Bauteile entstehen Trocknungsflecken, die nachgelagerte Montagen wie z. B. Lötprozesse erschweren oder sogar unmöglich machen. Gleichzeitig trocknen die Bauteile nicht in der geforderten Taktzeit von sieben Minuten rechtzeitig ab.
Neben dem konstant hohen Energieverbrauch stellt auch das Handling der stark aufgeheizten Bauteile eine große Herausforderung dar.
Kondensationstrocknung als „Gamechanger“
In einer einjährigen Entwicklungs- und Testphase und in enger Zusammenarbeit mit dem Allgäuer Trocknungsanlagenbauer Harter wurde die komplette Trocknung am Produktionsstandort Helmbrechts auf zwei Gestelltrockner umgerüstet. Um die neue Trocknungstechnologie bestmöglich auf unsere Projekte, Werkstoffe und Kundenvorgaben auszulegen, wurden zunächst einige Musterteile im Harter Technikum auf unterschiedliche Parameter erfolgreich getestet.
Das Ergebnis: Dank ihres alternativen physikalischen Ansatzes kann die Kondensationstrocknung in einem niedrigeren Temperaturbereich zwischen 40 °C und 75 °C arbeiten. Modernste integrierte Wärmepumpentechnik macht das System effizienter als andere Trocknungsverfahren. Entsprechend liegen Trocknungszeiten oftmals sogar deutlich unter den vorgegebenen Taktzeiten. In unserem Fall ergeben sich bei einem Wärmeeinsatz von nur 60 °C Trocknungszeiten von lediglich vier Minuten – ganz ohne Flecken.
Kaum Energieverlust
Beide Trockner sind aus Polypropylen gefertigt und verfügen über ein automatisches Deckelsystem, das sich ausschließlich zum Ein- und Ausfahren der Warenträger öffnet. Wertvolle Wärme bleibt während der Trocknung im System, weder Abluft- noch Feuchtebelastungen können entstehen.
Aufgrund der Ergebnisse im Vorfeld entschieden wir uns gemeinsam mit Harter die Trocknung bei 60 °C einzustellen. Dank der kurzen Trocknungszeiten und geringeren Temperatur wird eine starke thermische Beanspruchung und Aufheizung des Bauteiles verhindert. Die Oberflächen erwärmen sich auf lediglich 45 °C und können somit unmittelbar weiterverarbeitet werden.
Auch energetisch überzeugt die Kondensationstrocknung mit ihrer Wärmepumpentechnologie: die Nennleistung im Produktionsbetrieb beträgt für die neu eingerichtete Anlage je System insgesamt 6,8 kW beziehungsweise 8,2 kW. Ein enorm niedriger Wert, bei einer deutlichen Qualitätssteigerung.
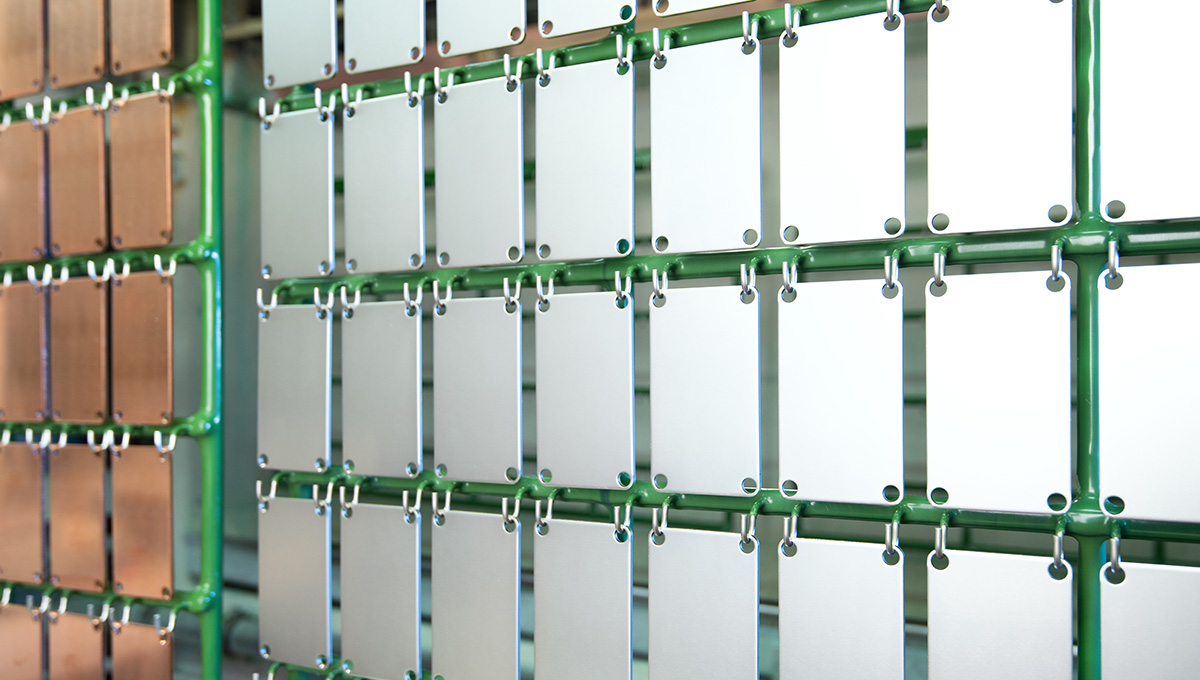
Komplett abluftfrei
Die neuen Trockner verfügen über ein integriertes Umluftsystem mit einer individuellen Luftführung. Dabei sind je Trockner vier beziehungsweise sechs Umluftventilatoren eingebaut, die den passenden Luftvolumenstrom erzeugen. Alle Trockner sind mit speziellen Abblasdüsen ausgestattet, die beim Einfahren des Warenträgers die erste große Wasserfracht von den oftmals komplexen Bauteilen abblasen.
In einem vollständig geschlossenen Kreislauf wird die benötigte Prozessluft zunächst in einem Air genex®-Entfeuchtungsmodul aufbereitet, anschließend mit einer hohen Geschwindigkeit über die Teileoberfläche geführt. Diese trockene Luft nimmt die Feuchte sehr schnell auf und kühlt diese im Entfeuchtungsmodul, bis das Wasser kondensiert. Die Luft wird wieder erwärmt und im Kreislauf zurück in den Trockner geführt. Diese Kombination aus geschlossenem Kreislauf und kompletter Abluftfreiheit ist in dieser Art und Weise einzigartig am Markt.