Optimale Hafteigenschaften dank Drehteller-Verfahren und individueller Temperierung.
Neben der Fertigung von reinen Silikonfertigteilen nutzen wir unseren Vorsprung in der Mehrkomponentenfertigung für eine äußerst komplexe Verbundtechnologie: das 2K-Spritzgießen mit Flüssigsilikon. Wo heute in einem hochautomatisierten Prozess anspruchsvolle Thermoplastteile mit Metalleinlegern und LSR-Dichtungen für die Automobilindustrie entstehen, wurde 2010 erstmals der Grundstein für unsere heutige Paradedisziplin gelegt.
Neben dem konstant hohen Energieverbrauch stellt auch das Handling der stark aufgeheizten Bauteile eine große Herausforderung dar.
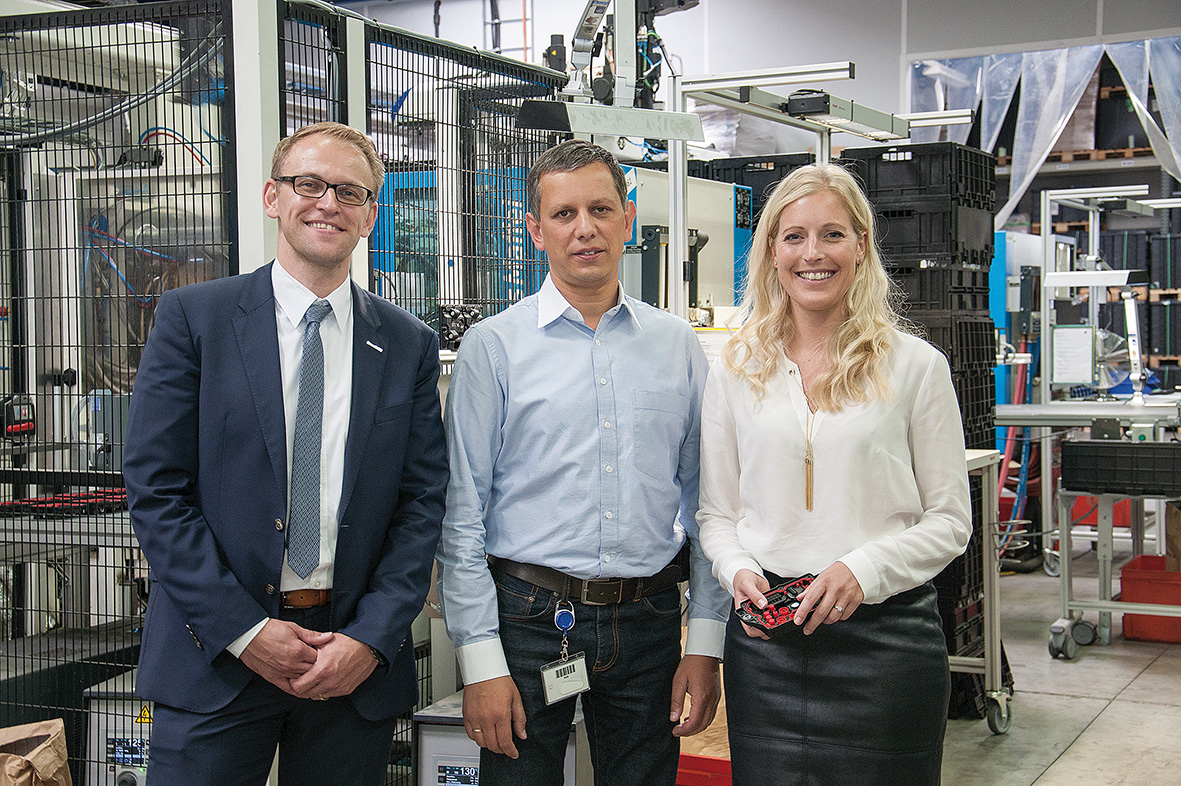
Erfolgreiches Teamwork (v.l.): Florian Eilhardt, Vertrieb Krauss Maffei, Reinhard Schneider , Betriebsleiter Rudi Göbel und Cordula Wieland, Produkt- & Technologiemanagement
Ein Pilotprojekt als Initialzündung für jahrzehntelange Entwicklungsarbeit.
In enger Zusammenarbeit mit dem Münchener Maschinenbauer Krauss Maffei entwickelten wir bereits 2010 ein Konzept für die Realisierung einer mehrlippigen Silikondichtung, die in eine Steuerplatine aus glasfaserverstärktem PA 6 integriert werden sollte. Zunächst erfolgten vereinzelte Tests auf einer 1K-Maschine, auf der erste Musterteile der Hartkomponenten gefertigt wurden. In einem 2. Schritt wurde die haftungsmodifizierte LSR-Dichtung direkt vor Ort bei Krauss Maffei angespritzt. Es zeigte sich, dass die unterschiedlichen Temperaturen und Haftungsaufbauten zu erheblichen Problemen führten. Entsprechend mussten wir in Bezug auf das Verfahren umdenken.
Aufgrund unserer Erfahrungen mit der Umsetztechnik und dem Hart-Hart-Spritzgießen, entschieden wir uns für die komplexere Drehtellertechnik in einem 2K-Verfahren. So konnten wir die klassischen Verzugsprobleme vermeiden und gleichzeitig die hohe Temperatur des Thermoplastteils mit nutzen, was sich wiederum positiv auf die Haftung und die LSR-Vernetzung auswirkte. Das Bauteil verbleibt in der Kavität, entsprechend reduziert sich die Schwindung und die Zykluszeiten können nochmals deutlich verkürzt werden.
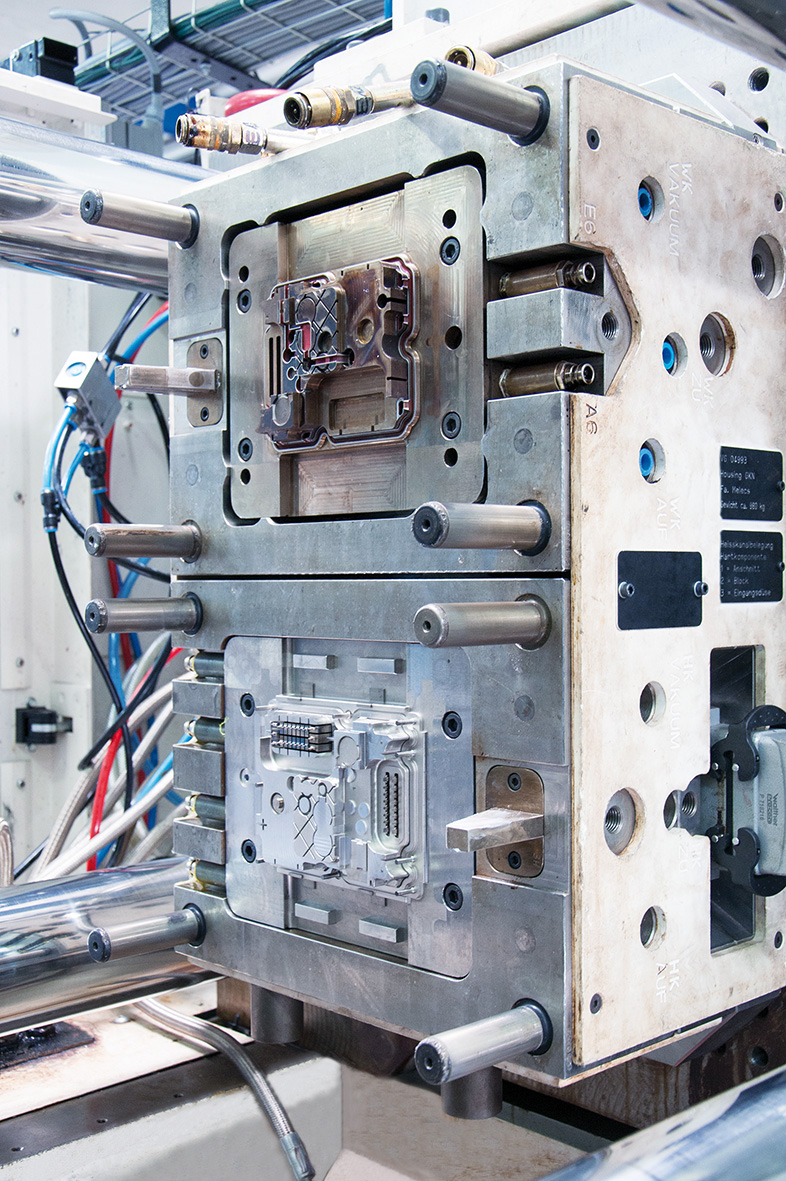
Thermische Trennung als Schlüssel.
Der Temperaturunterschied zwischen der Thermoplast-Kavität mit ca. 120 bis 140 °C und der Werkzeugtemperatur beim Einspritzen der Silikonkomponente mit ca. 200 °C stellt eine große Herausforderung beim Hart-Weich-Spritzgießen dar. Hier bedarf es besonderen Know-hows bei der Drehteller-Konstruktion und Medienführung, um den Wärmehaushalt optimal zu steuern. Die heißen und kalten Medien im Drehteller erfordern stetig hohe Abdichtungsebenen. Hinzu kommt die enorme thermische Belastung des Materials, die aus der konträren Ausdehnung der verschiedenen Temperaturbereiche resultiert.
Halbierte Silikon-Vernetzungszeit.
Die Kombination von Silikon und Thermoplast im 2K-Verfahren lenkt unseren Fokus zudem auf die unterschiedlichen Zykluszeiten beider Werkstoffe. Hier gilt es die deutlich längere Vernetzungszeit von LSR zu reduzieren und an die Zykluszeit des Thermoplasts anzupassen. Nur so können wir die Vorteile der 2K-Fertigung auch tatsächlich ausnutzen und den Prozess effizient gestalten.
Ursprünglich liegen die Mindestvernetzungszeiten eines LSR Elastosils bei einer Härte von 50 Shore A laut Herstellerangaben bei 120 bis 180 Sekunden. Dank spezieller Werkzeugkonstruktionen und konturnahen Temperierungen mit Flüssigmedien gelingt es uns, Teile mit lediglich 50 bis 60 Sekunden Zykluszeit bei gleich guter Vernetzung zu fertigen. Ein klarer Vorteil in puncto Prozesseffizienz.
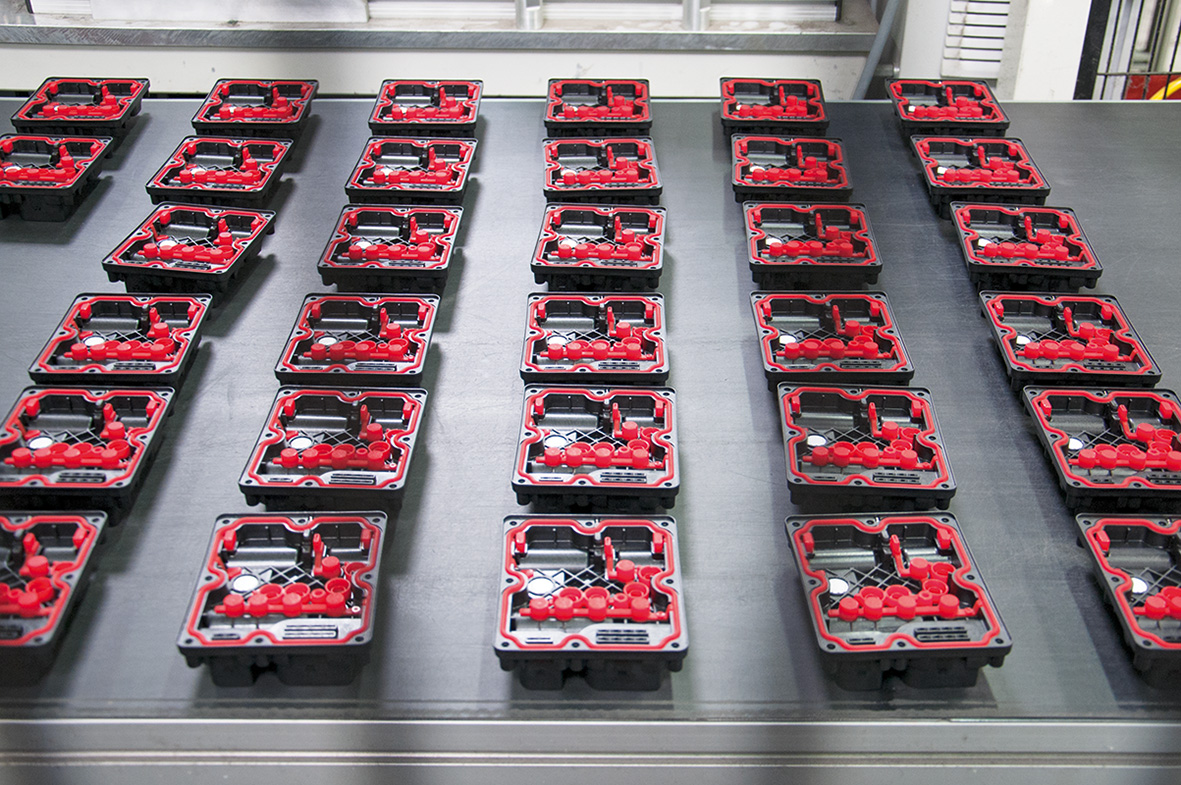
Erfahrung gefragt.
Die Haftungseigenschaften des Silikons werden immer auch durch die Materialschwankungen des Polyamids beeinflusst. Dabei ist es äußerst schwierig, diese vorab im Rahmen der Eingangskontrolle festzustellen. Selbst geringe Abweichungen bei der Farbdosierung können zu Viskositätsänderungen führen. Zwar lassen sich diese durch die Prozessparameter etwas ausgleichen, allerdings können wir die Chargenunterschiede oft nur mit viel Erfahrung und dem nötigen „Spiel“ so anpassen, dass die Prozessstabilität chargenübergreifend gegeben ist.
Heute sind wir in der Lage, in einem vollautomatisierten Prozess komplexe Automotive Gehäuseteile mit einem Glasfaseranteil von 30 % und LSR mit einer Härte von 50 Shore A zu produzieren – bestückt mit Metalleinlegern und Membranen, in einer Auflage von 10.000 Stück am Tag.